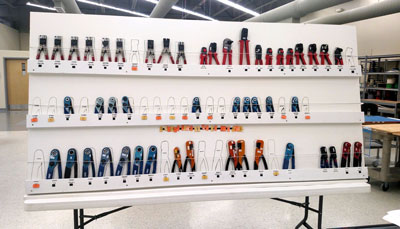
By analyzing the process of constructing an important cable assembly over the course of several years, lean-based changes have resulted in significant improvements.
In 2012, a group of employees from Ideal Aerosmith participated in an Impact Dakota training course. As part of the session, they held a Kaizen Event – a short-term project aimed at improving a specific part of an organization’s processes. For this test situation, the group chose to observe a technician putting together an electrical cable assembly that is often used in Ideal Aerosmith’s motion tables. As part of their observation, the working environment at Ideal Aerosmith was recreated, and the group diagrammed the technician’s actions, mapping out the time and distance of his every move.
“What we discovered was eye-opening,” says Todd Johnson, Ideal Aerosmith’s director of quality assurance and a participant in the training course. “We couldn’t believe how many times the assembler had to get up to get what he needed.”
Once the observation test was complete, the Ideal Aerosmith team brainstormed ideas to improve the process, including organizing tools so that they were easier to find and relocating materials closer to the assemblers to minimize the time spent walking back and forth. One of the more significant changes that Ideal Aerosmith put into effect was empowering assemblers to self-inspect crimps. “Typically, assemblers are required to have another assembler perform the in-process inspection,” says Johnson, “ but we thought that if someone is trained and certified to inspect someone else’s work, they should be able to look at their own.”
While this Kaizen Event took place nearly four years ago, the results are just now becoming clear. “When we look back at the average time it took to build the cable assemblies, the first five builds took about 6.7 hours each,” says Johnson. “The last five builds took an average of four hours per assembly. That’s a 40 percent reduction in labor hours.” Furthermore, when Johnson investigated how long the very first build took in July 2010, it was completed in 9.4 hours, versus the most recent build performed in March 2015, which took only 1.4 hours. The assemblies were all completed by employees with the same skill level.
“A small improvement by itself is nothing,” says Johnson, “but when we continuously make small improvements, they add up to something major. This analysis has shown that what we’re doing with lean matters. Our efforts are indeed producing results, and remarkable ones at that. We’re reducing our costs and our lead time, and the best part is that we are passing on those efficiencies to our customers.